Applications of Binder Jetting Technology (BJ) in Innovative Metal Powder Manufacturing
In the field of additive manufacturing, Binder Jetting Technology (BJ) is becoming a key force driving industrial innovation. The case of GKN Group shows that BJ technology not only enables the rapid manufacturing of complex parts but also brings significant advantages in cost control and product innovation.
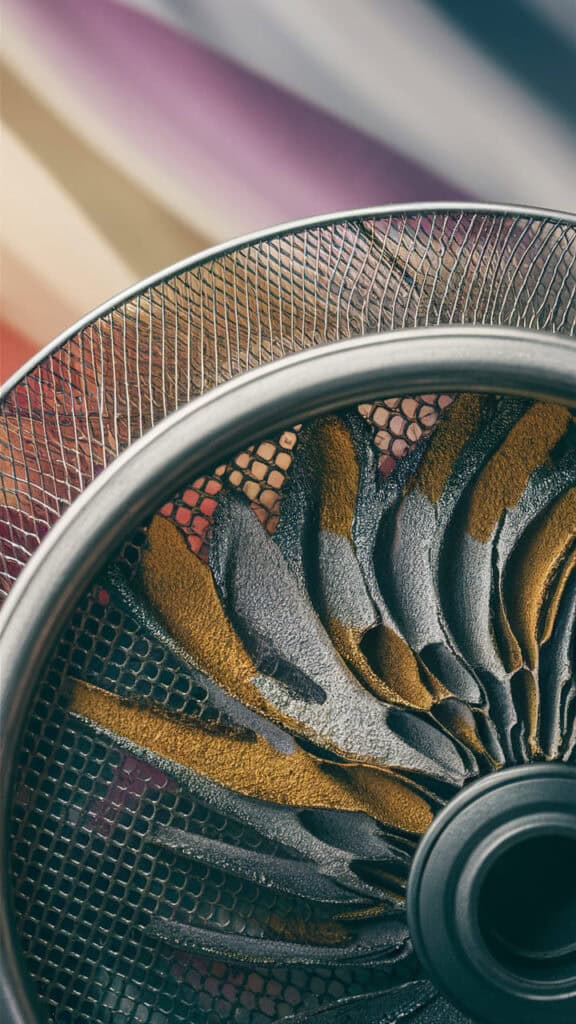
1.Overview of Binder Jetting Technology (BJ):
BJ technology involves precision jetting of liquid binders to bond powder particles layer by layer, forming a three-dimensional solid.
This process enhances production efficiency and provides greater design flexibility.
Compared to traditional manufacturing methods, BJ technology reduces material waste, shortens product development cycles, and allows for more complex geometric designs.
2. Support-Free Metal 3D Printing
GKN Additive has demonstrated the potential of BJ technology in mass production through its continuous improvement and research.
GKN Group, through its GKN Additive brand, has achieved significant success in manufacturing parts and products for large civilian aircraft, transport aircraft, automobiles, agricultural machinery, etc.
Notably, the collaboration with Schneider Electric in developing the ComPacT® circuit breaker filter project showcased the application of BJ technology in manufacturing high-performance structural components.
3. Successfully Tested Powder Materials:
Our team has successfully tested a range of high-performance metal powders, including:
316L Stainless Steel: Excellent corrosion resistance and formability, widely used in chemical, food processing, and medical device industries.
17-4PH Precipitation Hardening Stainless Steel: Known for its high strength and corrosion resistance, it is suitable for demanding aerospace and nuclear industry applications.
H13 Tool Steel: With its excellent thermal stability and wear resistance, it is commonly used for molds and die-casting tools.
M2 High-Speed Steel: High red hardness and wear resistance make it ideal for manufacturing high-precision cutting tools.
A2 and D2 Tool Steels: High wear resistance and impact toughness, suitable for manufacturing long-life cold work dies.
Copper Powder: Due to its superior electrical and thermal conductivity, it sees widespread application in the electronics industry.
WC12Co and WC17Co Hard Alloys: High hardness and wear resistance, suitable for manufacturing cutting tools and wear-resistant parts.
Inconel 625: Exceptional high-temperature strength and corrosion resistance, suited for high-temperature working environments.
Silver Powder: Known for its high electrical and thermal conductivity, widely used in electronics and thermal management applications.
The application of these powders in BJ technology not only enhances product performance but also broadens design possibilities.
4.Testing and Validation of Powder Materials
Through a series of rigorous tests, we have validated the performance of these powder materials in BJ technology, including their mechanical strength, heat resistance, and corrosion resistance.
The test results indicate that these powder materials meet high-performance requirements for industrial applications.
The test results indicate that these powder materials meet high-performance requirements for industrial applications.
5. Industrial Application Prospects
The combination of BJ technology with these high-performance powders heralds a new era in industrial manufacturing.
From aerospace to medical devices, the application prospects are vast, offering unprecedented opportunities for innovation.
BJ technology can provide solutions for complex parts that are difficult to achieve with traditional manufacturing methods, and offers a platform for the development and application of new materials.
6. Conclusion
The development of BJ technology and our successful testing of high-performance powders showcase the potential of additive manufacturing in driving industrial progress.
As technology continues to mature, we look forward to seeing more innovative products and solutions emerge to meet the growing market demand and drive industrial innovation.